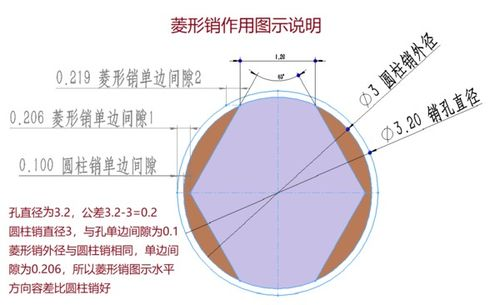
一、工件定位的基本原则
工件定位是确保加工过程中工件准确放置的关键步骤。根据六点定位原则,通过合理设置支撑点,限制工件在空间中的六个自由度,从而实现精确定位。在实际操作中,我们需要考虑以下因素:
1. 定位基准的选择,应选择与加工要求相适应的基准面;
2. 定位元件的精度,确保定位元件的加工精度;
3. 定位元件的布局,合理布局定位元件以提高定位稳定性。
二、夹具的选择与应用
夹具是工件定位与固定的工具,正确的夹具选择对于保证加工质量至关重要。在选择夹具时,应考虑以下方面:
1. 夹具的结构应与工件形状和尺寸相匹配;
2. 夹具的定位精度应满足加工要求;
3. 夹具的稳定性,确保加工过程中工件不会移位;
4. 夹具的操作便利性,提高生产效率。
三、工件定位误差分析
工件定位误差是影响加工精度的关键因素之一。常见的定位误差包括基准面误差、定位元件误差和夹具误差等。通过分析定位误差的来源,我们可以采取相应措施进行优化,提高定位元件的加工精度、优化夹具设计等。
四、提高工件定位精度的方法
提高工件定位精度是提高加工质量的关键。以下是一些有效的方法:
1. 优化定位基准,选择合适的基准面;
2. 提高定位元件的精度,使用高精度定位元件;
3. 改进夹具设计,提高夹具的稳定性和精度;
4. 实施在线检测,及时调整加工参数。
五、工件定位与夹具的未来发展趋势
随着科技的发展,工件定位与夹具技术也在不断创新。未来发展趋势包括:
1. 智能化,通过引入传感器和控制系统,实现夹具的自动调整和优化;
2. 高精度,不断提高定位元件和夹具的精度,满足高精度加工需求;
3. 模块化,设计模块化夹具,提高夹具的适用性和灵活性。